The recycling of industrial waste from food production is an important component of sustainable development. A variety of the food industry waste of plant origin may and is reused as food additives, soil fertilizers, for biogas production, etc. In this way, alcohol distillery stillage [1], brewer’s spent grain [2], coffee production waste [3], and others are being reused.
Apple pulp or apple pomace produced at canning and processing factories is no exception and has a wide range of secondary use. There is information about the use of apple pomace as a food additive for sausages [4] and nuggets [5], which are additionally enriched with extra fiber. Apple pomace is also used to create specialized apple flour [6], as well as an additive to flour [7], including gluten-free ones [8]. Another area of focus is the targeted production of pectin [9], which is a valuable stabilizer, thickener and emulsifier in the food industry. In addition, pectin has biomedical properties, such as toxin elimination and lowering blood cholesterol levels [9].
Apple pulp can be used to produce biodiesel [10] and bioethanol [11]. Also, the bioconversion of apple pomace into biogas is being developed in various ways, which makes it possible to produce renewable energy in the form of methane – the effect of carbon conductive materials and trace element additives on improving biogas production is being studied [12], anaerobic digestion with meat industry residues [13] or together with animal slurry and other plant origin waste [14].
Apple pomace is attractive for the production of biochar [15], which can be even used to create Na-ion batteries [16]. A possible directions are using of apple pomace for the synthesis of biopolymers [17] and biobased films [18].
Given the high lignin content of apple pomace, which is approximately 15÷20 % [19], and the authors’ previous positive experience of using lignin-containing plant waste as a raw material for the creation of alternative solid fuel (alcohol distillery stillage [1], brewer’s spent grain [2], coffee production waste [3]), it was appropriate to assess this possibility for apple waste.
However, apple pulp, like most food industry waste of plant origin, has an excessively high moisture content (< 65%), which reduces its shelf life to several days [20]. Therefore, this product must be pre-dried for further use. Since the cost of apple pomace is relatively low as an industrial waste, the main cost item is the preliminary raw material preparation – the drying process [21]. Thus, the purpose of the study was to evaluate the aspects related to the preliminary preparation of plant material – apple pomace, the possibility of using it as an energy source and the overall efficiency of the process.
For the research, it was used apple pomace obtained on the production line of a local juice production enterprise in Lviv region, Ukraine.
Methods for determining the moisture content and bulk density of raw materials are described in detail in [20]. The initial moisture content of the apple pomace was 83.06% wt. and the bulk density was 446.47 kg/m3.
The drying process of apple pomace was studied using the filtration drying method; the scheme and principle of operation of the laboratory installation are described in [21]. The study of the filtration drying kinetics of raw materials of plant origin, the derivation of generalized equations for the drying rate and duration were made following the theory and methodology described in [21].
The hydrodynamics study was performed using the same filtration drying installation [21], and the methodology for analysis and computer modeling is given in [22].
The calculation of technologically feasible parameters of filtration drying according to experimental data and the calculation of specific energy consumption for moisture removal were performed according to the methodology described in [23].
Calorimetric studies were carried out to determine the main characteristics of the formed and unformed material (higher calorific value, ash content, moisture content) in accordance with the requirements of the State Standards of Ukraine: DSTU EN 14918:2016 (EN 14918:2009, IDT). Solid biofuels. Method for determination of calorific value, DSTU ISO 18122:2017 Solid biofuels. Method for determination of ash content, DSTU EN 14774-2:2013. Solid biofuels. Determination of moisture content. The method of burning samples is described in [1].
The dried apple pomace was pressed in a P474A hydraulic press at a pressure of ≈1000 N/cm2 and a mold temperature of 150 °C for 60 s to obtain prototypes of solid fuel briquettes [1].
In order to estimate the energy consumption for the preliminary drying of apple pomace, it was necessary to perform experimental studies of the kinetics of filtration drying, which was chosen because of its efficiency confirmed by authors [21], [23]. Three series of experiments were conducted, the peculiarity of which was the change of a certain process parameter – the thermal agent temperature T, the thermal agent filtration rate v0, the layer height of the wet material H.
When one of the studied parameters was changed, the other two parameters remained unchanged. As a result, we obtained curves of changes in the moisture content of the stationary layer of apple pomace over time at different heights of the wet material (Figure 1), different temperatures of the thermal agent (Figure 2), and different velocities of its movement through the stationary layer of apple pomace (Figure 3). Additionally, the value of the equilibrium moisture content of apple pomace was determined, which was conditionally taken as the lowest value at a certain temperature: for 60 °C, 70 °C, 80 °C, and 90 °C, the values were 0.221, 0.201, 0.151, and 0.099 kg H2O ⁄ kg dry material, respectively.
Changes in the moisture content of a stationary layer of apple pomace over time at different heights of the stationary layer of wet material
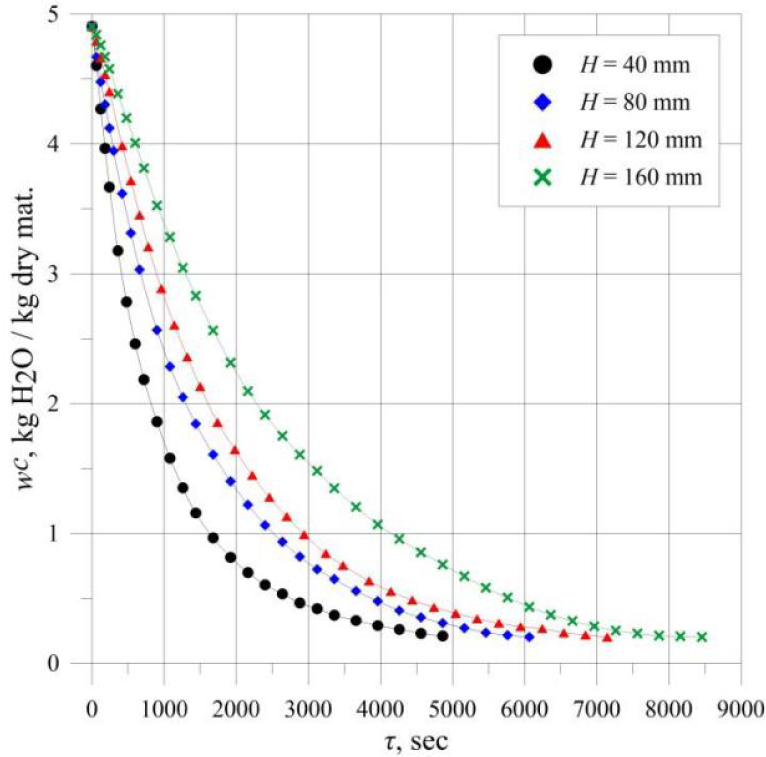
Changes in the moisture content of a stationary layer of apple pomace over time at different temperatures of the thermal agent
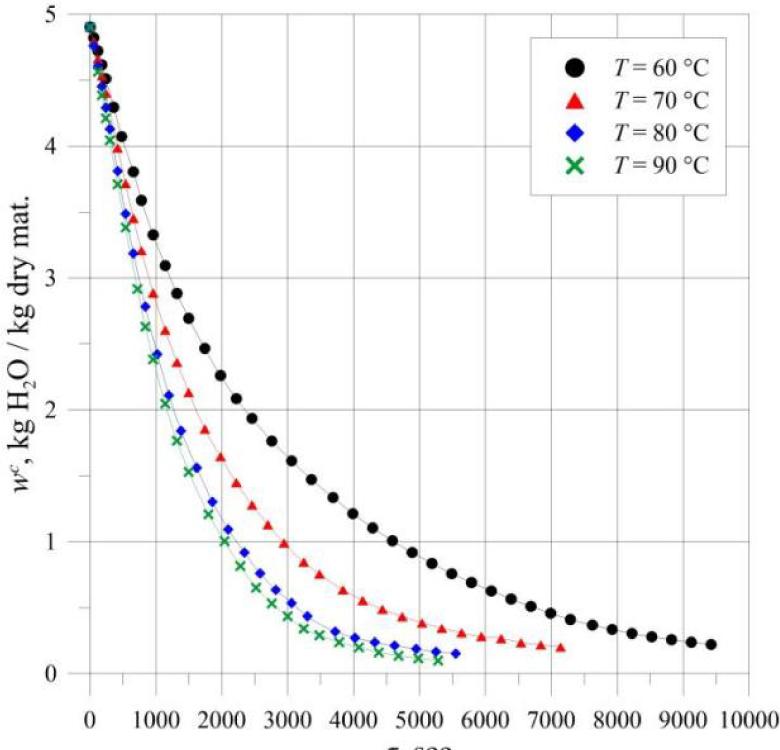
Changes in the moisture content of a stationary layer of apple pomace over time at different velocities of the thermal agent
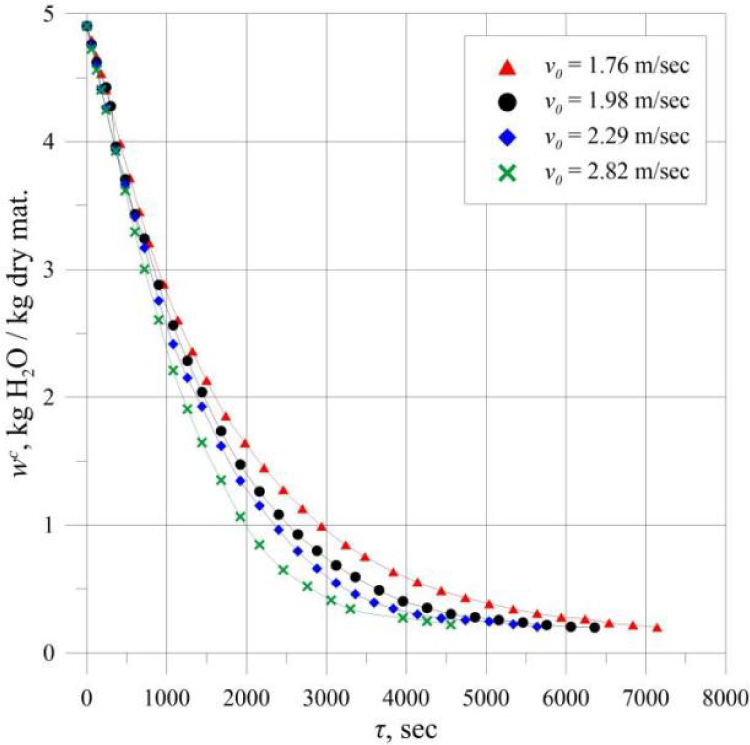
Graph-analytical method for determining the critical moisture content and the time of its achievement at different stationary layer heights of wet material
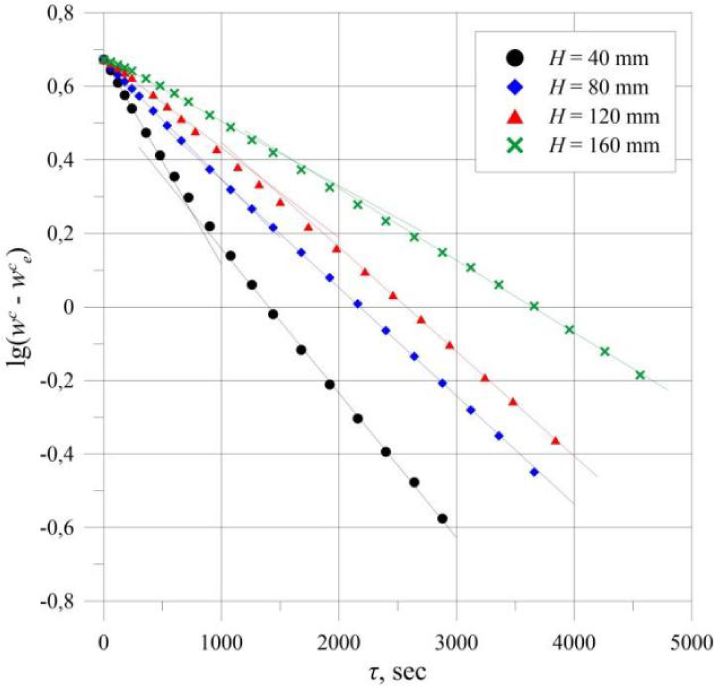
Graph-analytical method for determining the critical moisture content and time of its achievement at different temperatures of the thermal agent
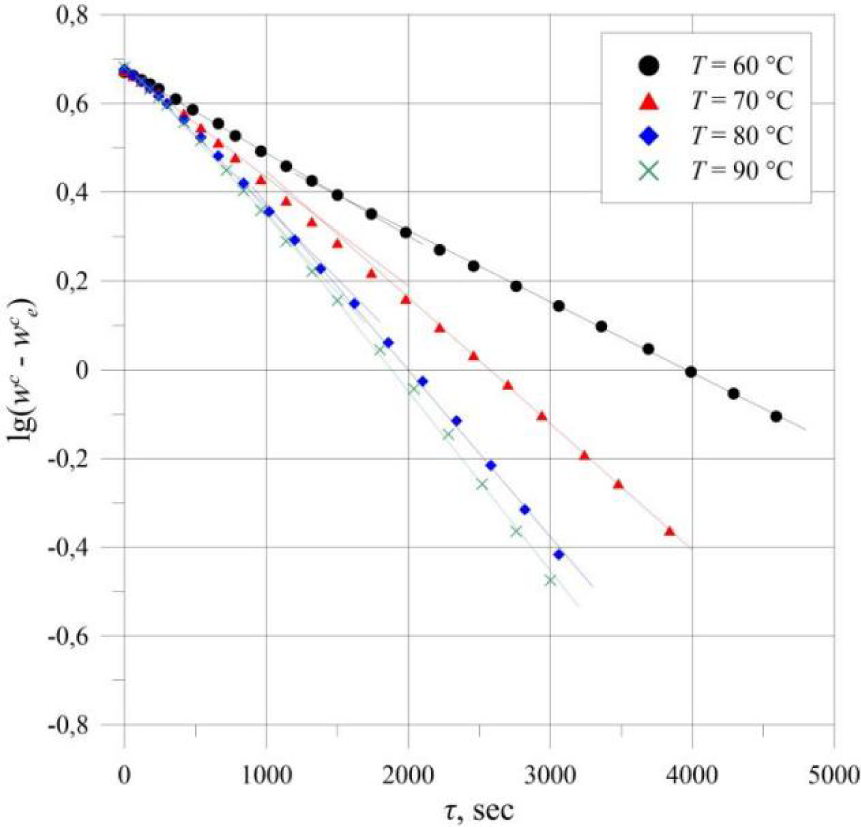
Graph-analytical method for determining the critical moisture content and the time of its achievement at different velocities of the thermal agent
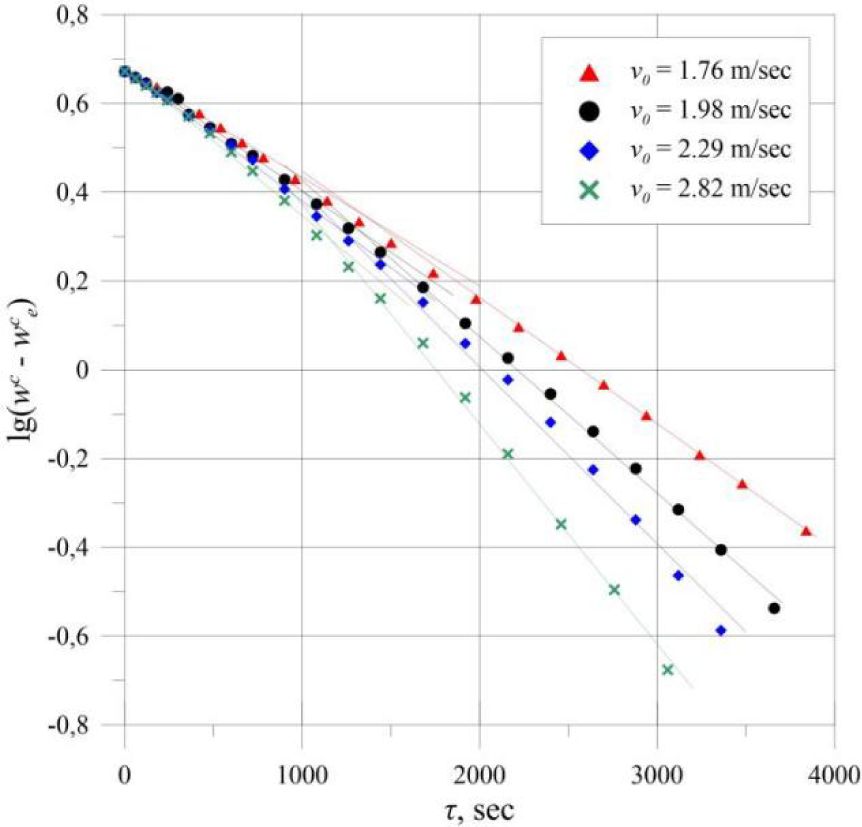
Using the graph-analytical method [21], the critical moisture content and the time of its achievement τcr were determined at different stationary layer heights of apple pomace (Figure 4), different temperatures of the thermal agent (Figure 5), and different velocities of the thermal agent (Figure 6). The results of the graphical analysis are given in Table 1.
Values of the critical moisture content of apple pomace and the time of its achievement τcr
H, [mm] | T, [°C] | v0, [m/sec] | lg (wc – ) | , [kg H2O ⁄ kg dry material] | τcr, [sec] |
---|---|---|---|---|---|
40 | 0.258 | 2.012 | 740 | ||
80 | 0.321 | 2.295 | 1070 | ||
120 | 70 | 0.348 | 2.429 | 1260 | |
160 | 1.76 | 0.387 | 2.639 | 1640 | |
60 | 0.385 | 2.648 | 1550 | ||
80 | 0.316 | 2.221 | 1140 | ||
90 | 0.299 | 2.090 | 1100 | ||
120 | 1.98 | 0.317 | 2.276 | 1310 | |
70 | 2.29 | 0.306 | 2.224 | 1250 | |
2.82 | 0.293 | 2.164 | 1160 |
According to the methodology of [21], using the graphical method, the kinetic coefficients a and η were determined for the first conditional drying period, the period of complete moisture saturation (Figure 7). The results of the graphical determination of the kinetic coefficients are given in Table 2.
Determination of the kinetic coefficients a and η in the first conditional drying period
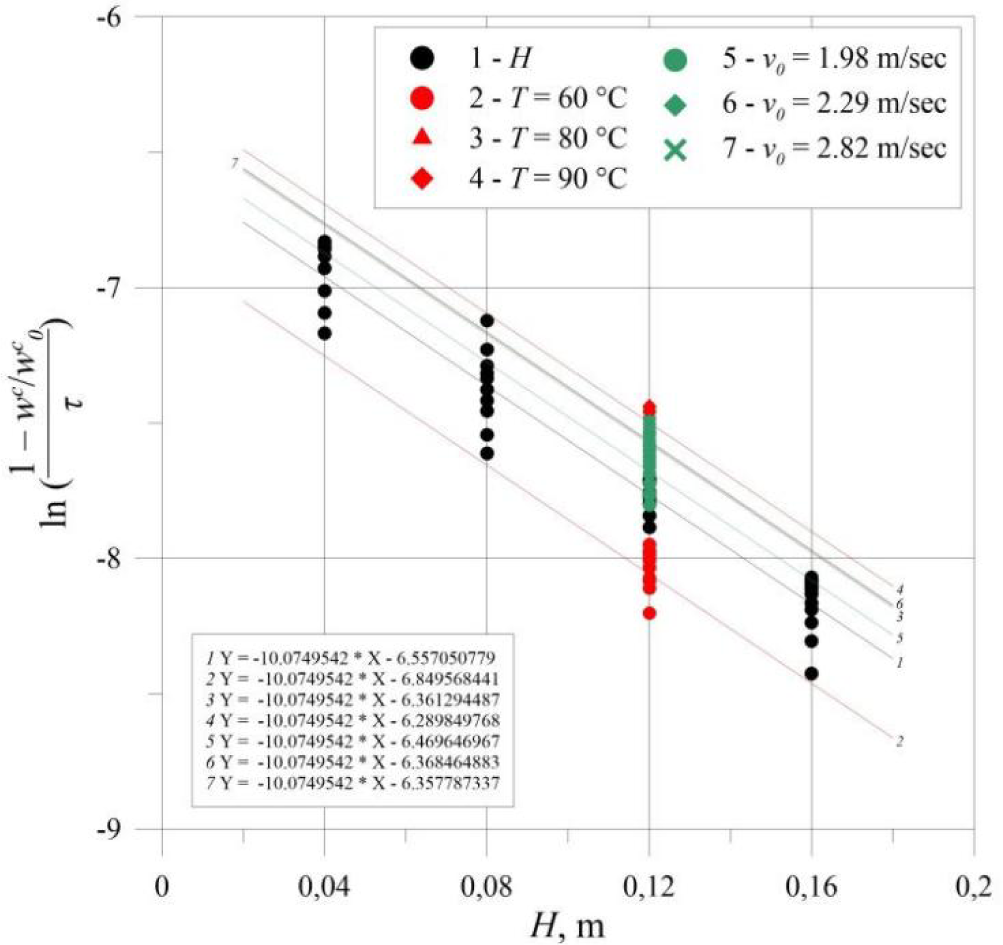
Dependence of the kinetic coefficients a and η on the parameters of the filtration drying process of apple pomace
No. of the line | H, [mm] | T, [°C] | v0, [m/sec] | a, [1/m] | ln (η) | η, [1/sec] |
---|---|---|---|---|---|---|
1 | 40 | 70 | - 6.557050779 | 0.001420068 | ||
80 | ||||||
120 | ||||||
160 | 1.76 | |||||
2 | 120 | 50 | 10.075 | - 6.849568441 | 0.001059913 | |
3 | 80 | - 6.361294487 | 0.00172713 | |||
4 | 90 | - 6.289849768 | 0.001855039 | |||
5 | 70 | 1.98 | - 6.469646967 | 0.001549773 | ||
7 | 2.29 | - 6.368464883 | 0.00171479 | |||
8 | 2.82 | - 6.357787337 | 0.001733197 |
Having determined the coefficients A = 1.237×10-5, m = 1.06, n = 0.422 to express the kinetic coefficient η in the first drying period of complete saturation of the thermal agent with moisture [21], write down an expression to describe the kinetics of filtration drying of apple pomace in this drying period:
(1)
To generalize the regularities of the filtration drying rate of apple pomace in the second conditional drying period, graphical dependencies are constructed to determine the drying coefficient K (Figure 8 - Figure 10). The coefficient K allows us to find the relative drying coefficient χ at a known value of the drying rate in the second conditional period of partial saturation of the thermal agent with moisture N [21]. The results of the graphical analysis are summarized in Table 3.
Determination of the coefficient K at different stationary layer heights of wet material
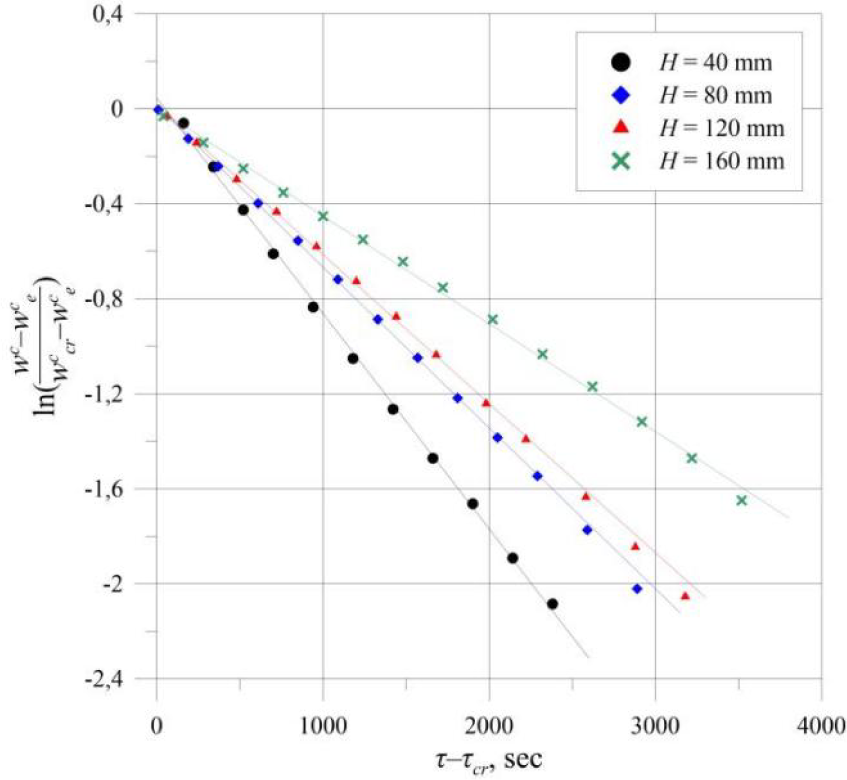
Determination of the K coefficient at different temperatures of the thermal agent
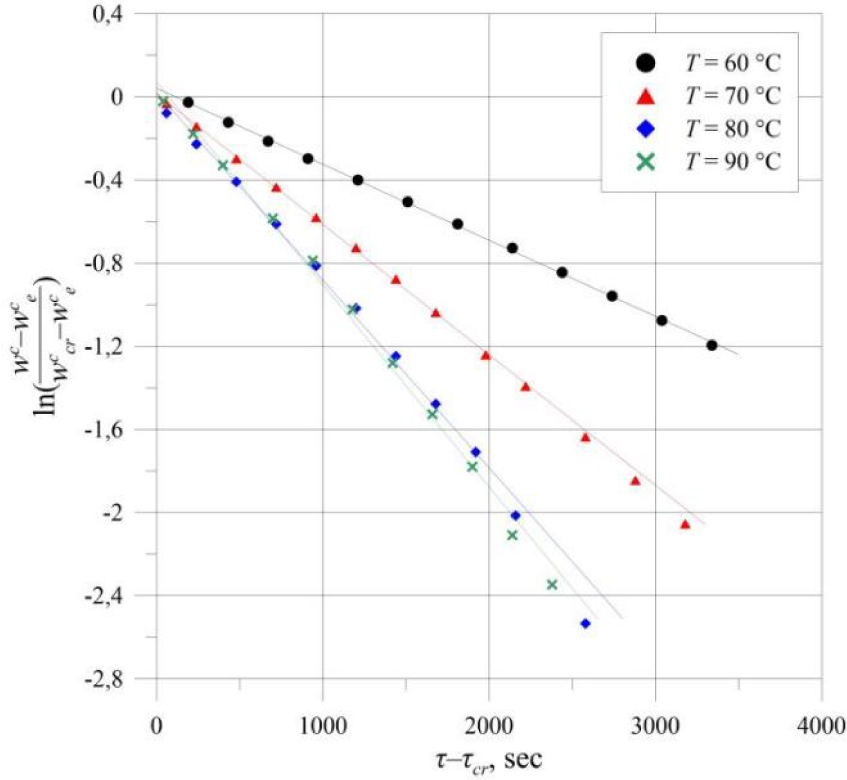
Determination of the coefficient K at different velocities of the thermal agent
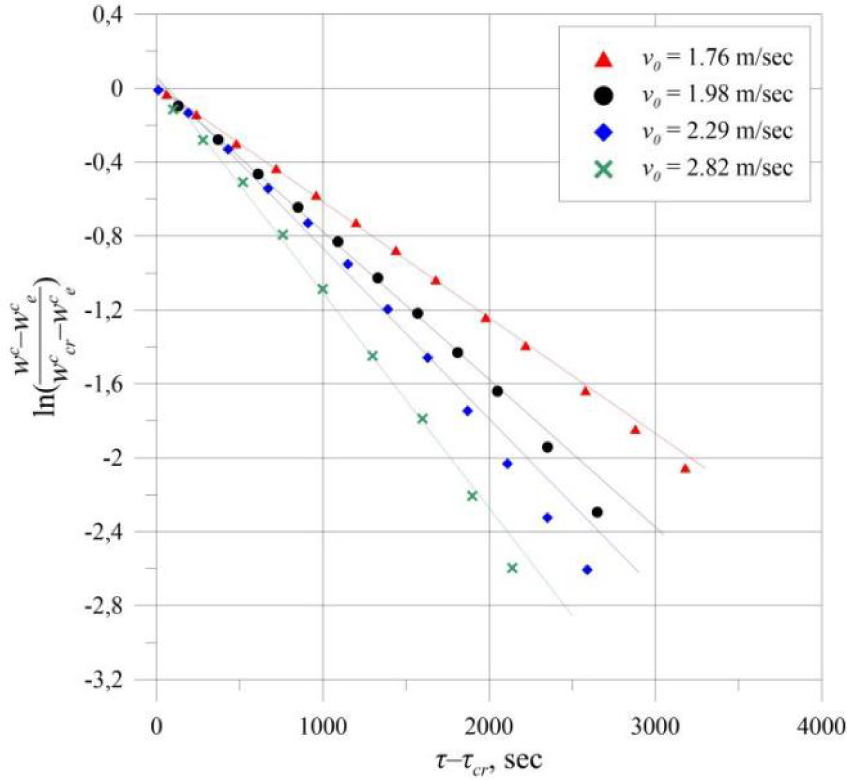
Dependence of drying coefficient K on drying rate N for filtration drying of apple pomace
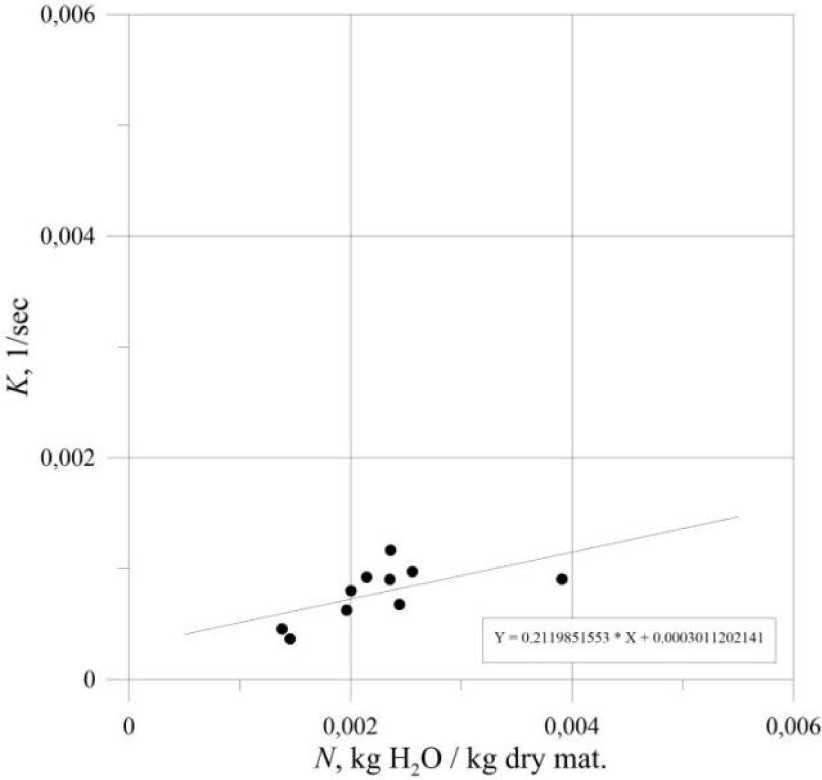
Dependence of the coefficients K and N on the parameters of the filtration drying process of apple pomace
H, [mm] | T, [°C] | v0, [m/s] | K, [1/s] | N, [kg H2O / kg dry material] |
---|---|---|---|---|
40 | 70 | 0.0009071688471 | 0.003910464 | |
80 | 0.0006770846801 | 0.002439947 | ||
120 | 0.0006274985227 | 0.001964300 | ||
160 | 1.76 | 0.0004538715003 | 0.001382160 | |
120 | 60 | 0.0003658081744 | 0.001455495 | |
80 | 0.0009031114463 | 0.002353524 | ||
90 | 0.0009736405255 | 0.002558198 | ||
70 | 1.98 | 0.0008000624044 | 0.002006120 | |
2.29 | 0.0009234367078 | 0.002144014 | ||
2.82 | 0.001165361066 | 0.002362084 |
The graphical dependence K = f (N) (Figure 11) indicates that for apple pomace the relative drying coefficient is χ = 0.211 kg H2O ⁄ kg dry material.
Thus, the generalized equation describing the drying rate in the period of partial saturation of the thermal agent with moisture will be as follows:
(2)
To assess the correctness of the derived mathematical dependencies (1) and (2), it was analyzed the distribution of the deviations of theoretically calculated values from the experimentally obtained ones. It should be noted that the analysis of the nature of the kinetic curves and the obtained set of experimental data indicates an increase in the deviation of theoretically calculated values from the experimental data after reaching a certain value of moisture content. This is due to the nature and type of raw materials - the heat consumption for the evaporation of bound moisture and heating of wet material, which increases with a decrease in the tangent of the slope of the kinetic drying curve to the abscissa axis and requires a correction factor for the second conditional drying period [23]. Thus, the authors recommend the use of eqs. (1) and (2) for the following range of moisture contents, where the error of conformity of experimental data to theoretically calculated ones is acceptable for calculations of drying equipment and does not exceed ~32 % (Table 4):
Recommended values of moisture content of apple pomace wc for the use of generalized dependencies for describing the filtration drying intensity of apple pomace
H, [mm] | T, [°C] | v0, [m/s] | wcrecommend, [kg H2O / kg dry material] |
---|---|---|---|
40 | 70 | < 0.21 | |
80 | < 0.64 | ||
120 | < 0.99 | ||
160 | 1.76 | < 1.21 | |
120 | 60 | < 0.63 | |
80 | < 1.09 | ||
90 | < 1.21 | ||
70 | 1.98 | < 1.26 | |
2.29 | < 1.34 | ||
2.82 | < 1.35 |
For the recommended values (Table 4), the largest absolute value of the deviation of theoretically calculated values relative to experimental data is 32.29%, the average value of this deviation is 7.60%. A graphical representation of the distribution of deviations of theoretically calculated values relative to experimental data is shown in Figure 12.
Distribution of deviations of experimental data to theoretically calculated ones for filtration drying of apple pomace
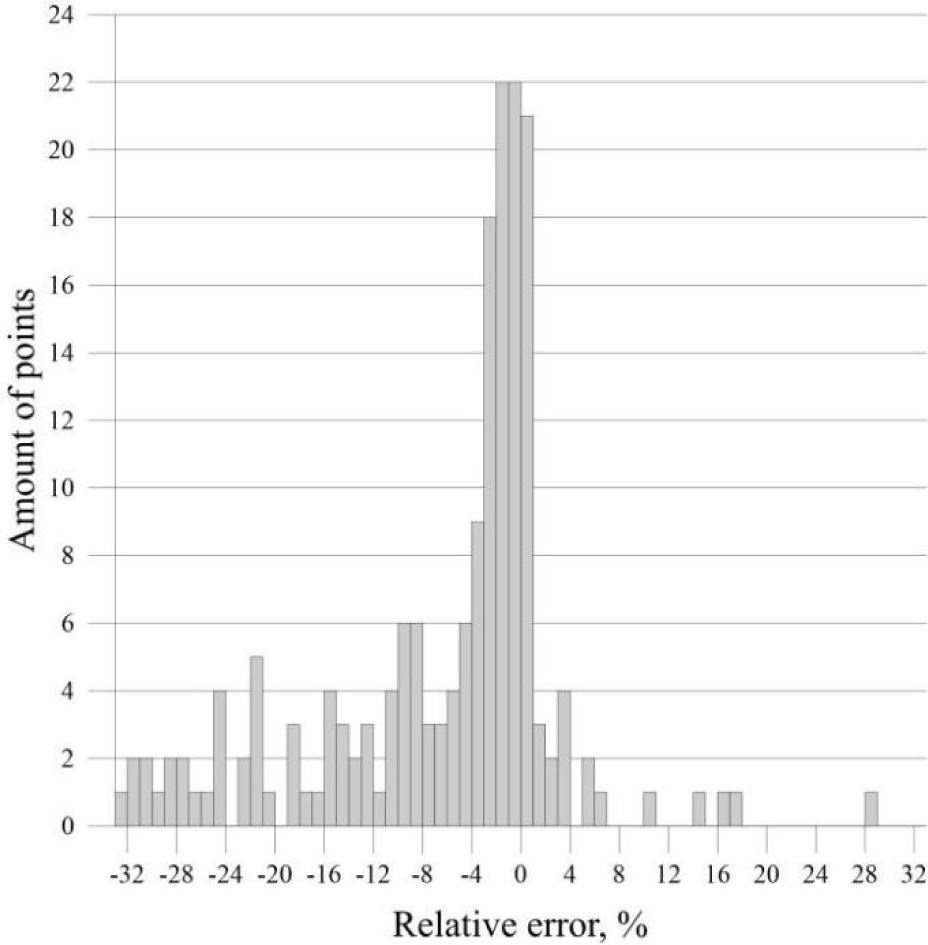
Eqs. (1) and (2) allow us to express the equations for determining the process duration in the first τI and second τII conditional drying periods, respectively:
(3)
(4)
The second important parameter for the calculation of filtration drying equipment is the hydraulic resistance of a stationary layer of material. Experimental studies were conducted to determine the effect of the fictitious flow rate v0 on the hydraulic resistance ΔP of the porous stationary layer of the material under study according to the method [22]. In addition, computer modeling was performed to generalize the obtained experimental values. Computer simulations of the hydrodynamics of the flow of the thermal agent were performed in the ANSYS Fluent 2022 R2 program [24], which is widely used for similar tasks [25], [26].
In accordance with the methodology of [22], the bulk density of dried apple pomace was experimentally determined to be 202.37 kg/m3 and the layer porosity of the studied material was 0.276.
The results of the hydrodynamics study of the thermal agent movement through a stationary layer of the studied material are presented in form of graphical dependence ΔP = f(v0) for the recommended values of the material layer height during drying under industrial conditions H = 80÷120 mm (Figure 13) [22].
Dependence of the fictitious velocity of the thermal agent on the change in the hydraulic resistance of the dried apple pomace layer at different heights
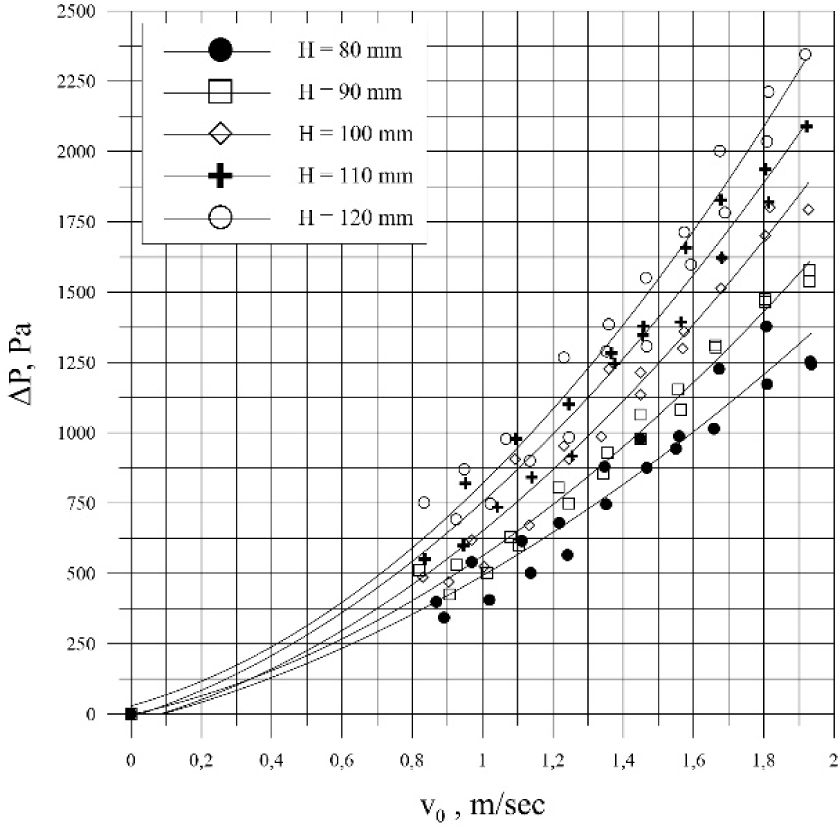
Graphical comparison of the obtained simulation values (––– red lines) of the hydraulic resistance of dried apple pomace with the experimental one (––– black lines) from the fictitious velocity of the thermal agent at different layer heights
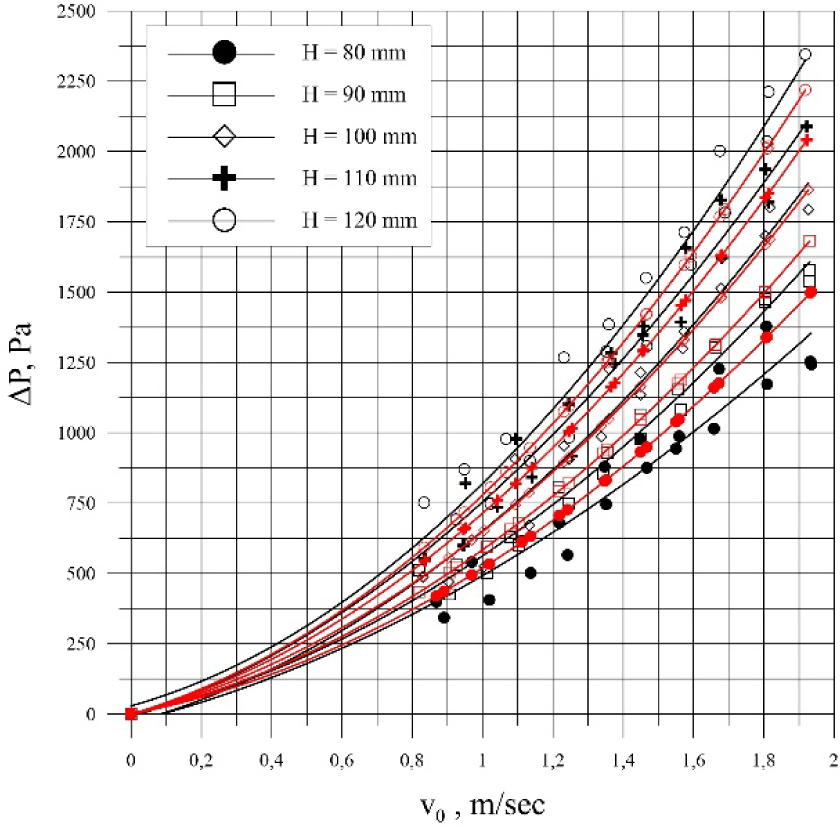
Table 5 shows the deviations of computer modeling from the values of hydraulic resistance obtained experimentally (Figure 14).
Deviation of the computer modeling from the experimental data for the studied stationary layer heights of apple pomace H = 80÷120 mm
Material layer height, [mm] | Average modeling error, [%] |
---|---|
80 | 12.72 |
90 | 6.73 |
100 | 7.08 |
110 | 6.80 |
120 | 8.07 |
Average value: | 8.28 |
Analyzing the simulation data, the average deviation for all experimental points is 8.28 % (Table 5). Taking into account the results of modeling according to the methodology [22], the pressure loss in the layer of apple pomace ΔP can be determined according to equation:
(5)
The calculation of the technologically feasible parameters of filtration drying at the experimental installation was performed according to the methodology described in [23], which was based on [27], [28]. The energy costs for heating the thermal agent to remove 1 kg of moisture and for overcoming the pressure drop to remove 1 kg of moisture were determined.
The determination of was based on the parameters of the filtration drying process [23], [27], as well as its duration, determined by Eqs. (3) and (4). The calculation of was based [23], [28] on the determination of pressure losses in a stationary layer of apple pomace according to Equation (5).
Taking into account the recommendations [1], it is advisable to dry the initial plant material to a moisture content of 14%, which in terms of moisture content is approximately wc ≈ 0.16 kg H2O/kg dry material. Based on the analysis of dependence (4) and the previously determined values of the equilibrium moisture content of apple pomace for different temperatures, it is possible to achieve the required moisture content at temperatures of 80 °C and 90 °C, since for these temperatures the values of are less than the final wc.
It should be noted that to calculate the time of filtration drying at temperatures of 80 °C and 90 °C for the second conditional period, it was necessary to take into account the additional heat consumption for the evaporation of bound moisture using the refinement coefficient KττII [23] – 0.45 and 0.55, respectively.
The results of calculating the technologically feasible parameters of filtration drying of apple pomace in the experimental installation are summarized in Table 6.
Initial parameters and results of energy consumption calculation for filtration drying of apple pomace at the experimental installation
№ | H, [m] | T1, [°C] | v0, [m/sec] | Gt.a., [kg/sec] | ΔP, [Pa] | τ, [sec] |
---|---|---|---|---|---|---|
1 | 0.12 | 80 | 1.76 | 0.013 | 1912 | 5804 |
2 | 0.12 | 90 | 1.76 | 0.013 | 1912 | 4544 |
№ | Qlabt.a., [kJ/kg H2O] | Nlabt.a, [kWh/kg H2O] | QlabΔP, [kJ/kgH2O] | NlabΔP, [kWh/kg H2O] | Qlab, [kJ/kgH2O] | Nlab, [kWh/kg H2O] |
1 | 23970.08 | 6.66 | 907.55 | 0.25 | 24877.62 | 6.91 |
2 | 21279.55 | 5.91 | 710.48 | 0.20 | 21990.02 | 6.11 |
Thus, the following parameters are taken as technologically feasible parameters of filtration drying of apple pomace: the height of the dried material layer H = 120 mm, the temperature of the thermal agent T = 90 °C, and the filtration velocity of the thermal agent v0 = 1.76 m/sec. With these process parameters, the energy consumption for removing 1 kg of moisture is 21990.02 kJ/kg H2O or 6.11 kWh/kg H2O.
If to estimate the industrial dehydration from the moisture content of raw materials of 83 % wt. to 14 % wt. by the filtration method and, for comparison, by the common method in a rotary dryer [29], according to the methodology [23], then in terms of dehydration of ≈ 1000 kg of apple pomace, the results will be as follows (Table 7):
Comparison of the calculation results of the drying process of apple pomace by the filtration method and in a rotary dryer for productivity for the initial material ~1000 kg
Indicator | Filtration drying | Rotary dryer |
---|---|---|
Productivity by source material G1, [kg/h] | 1045.58 | 1000 |
Total drying time τ, [sec] | 1.31 | 6.27 |
Total amount of energy required for the drying process N, [kWh] | 5338.08 | 5132.79 |
Total amount of energy required for the drying process Q, [kJ/kg of dry mat.] | 92977.11 | 93477.21 |
Total energy consumption for removing 1 kg of moisture for the drying process l, [kWh/kg H2O] | 6.36 | 6.40 |
Note that the heat capacity of apple pomace was calculated according to [30]. The parameters of the thermal agent were determined using the I-d state of humid air [31].
The data of the theoretical calculation of the filtration drying use in industry (Table 7) and the experimentally obtained data (Table 6) are close, which indicates the correctness of the calculation. Also, the calculation data of industrial drying methods indicate the efficiency of using filtration drying according to the indicators of specific energy costs for moisture removal and, above all, according to the duration of the process.
The calorimetric combustion method was used to determine three main indicators of the studied solid material (Figure 15) and the briquetted solid fuel sample created from it (Figure 16): residual moisture content, ash content, and higher calorific value in accordance with the State Standards of Ukraine [1].
Dried apple pomace
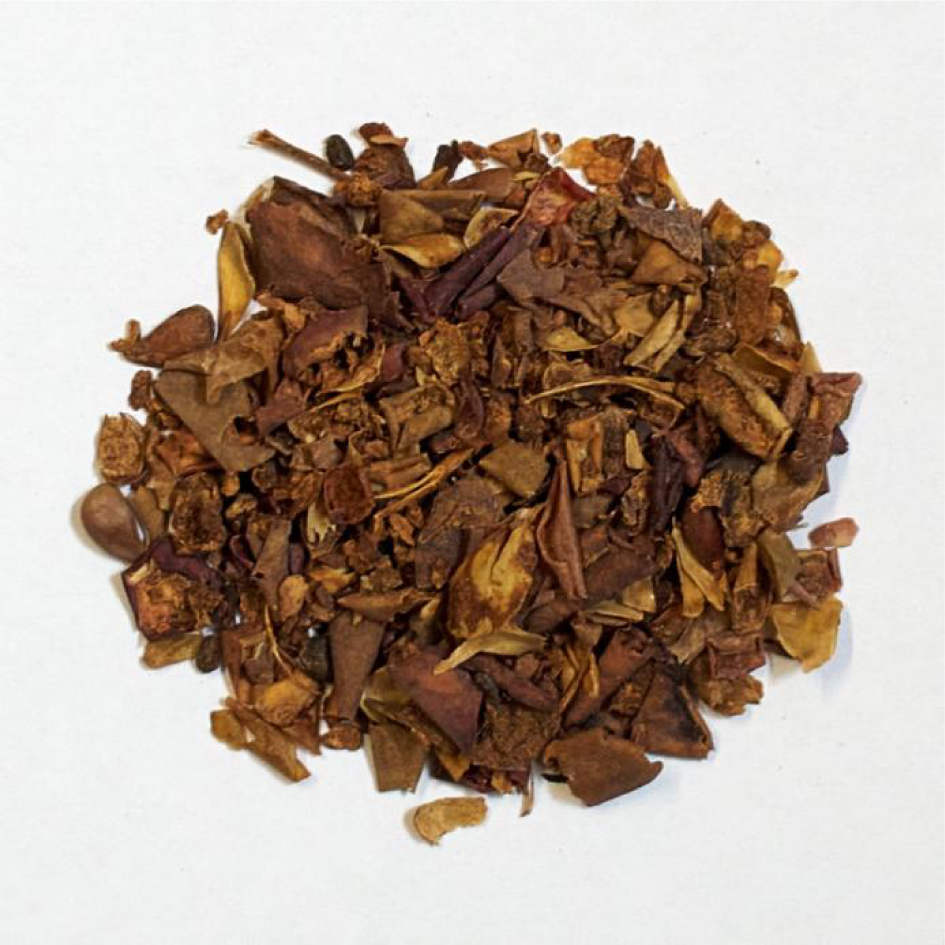
Briquetted sample of solid fuel obtained from apple pomace
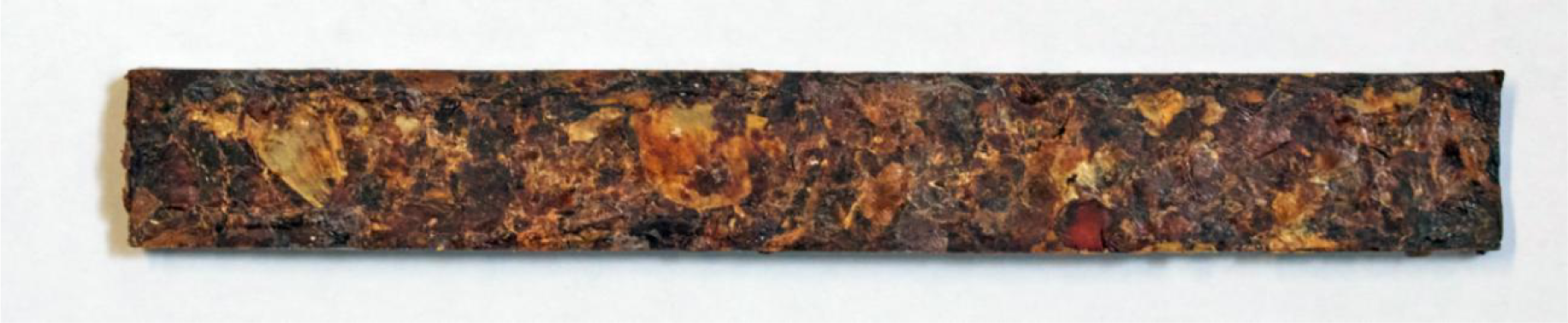
Due to the heterogeneity of the apple pomace composition, 3 parallel experiments were conducted to determine the average values. The results are presented in Table 8. Calorimetric studies of dried apple pomace showed the prospects of creating solid fuel briquette samples; briquetting conditions are described in the section “Experimental part”.
The moisture content of all the samples was < 1%. The values of calorific value, ash content, and residual moisture are close to or meet the requirements of European standards for solid fuels: German standard DIN 51731 (calorific value 15512÷19515 kJ/kg, ash content <1.5 %, residual moisture <12 %); Swedish standard SS 187120 (calorific value >16910 kJ/kg, ash content <1.5 %, residual moisture <10 %); etc. [32]. The obtained experimental data indicate the prospects of using apple pomace as an alternative solid fuel.
Results of calorimetric studies of apple pomace
№ | m*, [g] | ΔT, [V] | qthread, [J] | qHNO3, [J] | qsoot, [J] | Q, | Ash content, [% wt.] | |
---|---|---|---|---|---|---|---|---|
[kJ/kg] | [kcal/kg] | |||||||
Dried apple pomace | ||||||||
1 | 0.32980 | 0.59917 | 94.9 | 1.8 | 60.7 | 18691 | 4467 | 0.70 |
2 | 0.35766 | 0.64960 | 114.4 | 1.8 | 45.9 | 18598 | 4445 | 0.64 |
3 | 0.34307 | 0.61911 | 107.3 | 4.1 | 46.9 | 18486 | 4418 | 1.11 |
The average value: | 18592±59 | 4443±14 | 0.82±0.15 | |||||
Briquetted solid fuel sample | ||||||||
1 | 0.78093 | 1.4751 | 80.9 | 9.4 | 55.8 | 19502 | 4661 | 0.50 |
2 | 0.76471 | 1.4366 | 99.8 | 8.3 | 55.8 | 19371 | 4630 | 0.29 |
3 | 0.92478 | 1.7396 | 88.1 | 9.4 | 75.4 | 19442 | 4647 | 0.87 |
The average value: | 19438±38 | 4646±9 | 0.55±0.16 |
m – the mass of the substance that burned during the experiment; qthread, qampoule, qHNO3, qsoot – the amount of energy released during the combustion of cotton thread, terylene ampoule, the formation of a solution of nitric acid and soot formed, respectively; ΔT – true temperature rises in the calorimetric experiment.
Comparison of the obtained calorimetric combustion results of solid fuel samples obtained from apple pomace (Table 8) and the calculation of specific energy consumption for removing excess moisture from the material (Table 7) indicate the following: theoretically, 92977.11 kJ/kg of material should be spent for filtration drying of apple pomace to be able to obtain ≈ 19438 kJ/kg of energy as a result of using them as solid fuel. The values of energy consumed for the preliminary preparation of 1 kg of initial raw material exceed the potential energy that can be obtained as a result of burning 1 kg of the resulting fuel differ by 79.09 %. This balance can be corrected by using secondary heat at the factory to dry the raw materials, since the energy for heating the thermal agent makes up the largest part of the required energy consumption. It is also possible to consider the option of drying wet material in several stages, for example, initial mechanical pressing of moisture and filtration drying to the required moisture content of the raw material.
On the other hand, society lives not only in terms of economics, but also the need to improve the environmental situation in the world. The use of secondary raw materials of plant origin as an alternative solid fuel can replace the use of slowly renewable or non-renewable sources (such as wood and fossil fuels) and, at the same time, solve the problem of accumulating excessive amounts of industrial waste with a limited shelf life.
Of course, this estimate does not take into account energy costs for briquette production, warehouse rent, investments in new equipment, logistics, etc. However, given the availability and low cost of recycled materials, it can be argued that with a rational scheme of recycled material preparation, the use of apple pomace as an alternative solid fuel is a promising and rational area for practical use.
This paper analyzes the possibility of using industrial waste of plant origin from the food industry, apple pomace, as an alternative solid fuel. This work may be summarised in the following scheme (Figure 17):
The summary scheme of the study
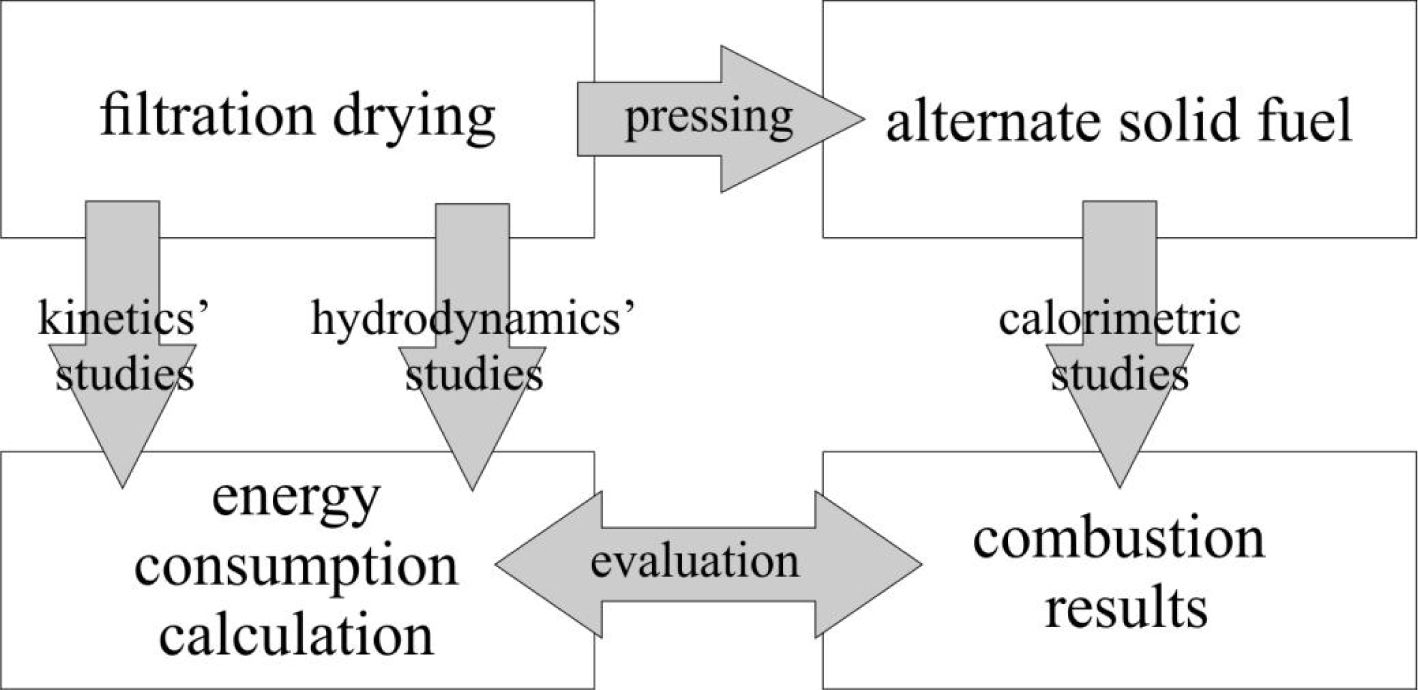
The aspects related to the preliminary preparation of the raw material were analyzed, due to its high initial moisture content of 83.06 % wt. It was proposed to dry apple pomace using a highly efficient filtration drying method. Based on experimental data, generalizing eqs. (1)–(4) describing the change in the moisture content of raw materials and the drying time were determined.
Based on experimental studies of hydrodynamics for technologically feasible heights of the stationary layer and computer modeling of the process, dependence (5) was determined, which helps to determine the hydraulic resistance during the filtration drying process.
The technologically feasible parameters of filtration drying were determined based on experimental data: the height of the dried material layer H = 120 mm, the temperature of the thermal agent T = 90 °C, and the velocity of the thermal agent v0 = 1.76 m/sec. With these process parameters, the energy consumption for removing 1 kg of moisture is 21990.02 kJ/kg H2O or 6.11 kWh/kg H2O.
An estimated calculation of the industrial drying of apple pomace from a moisture content of 83 % wt. to 14 % wt. by the filtration method in terms of drying ≈ 1000 kg of raw materials established the total energy consumption for removing 1 kg of moisture of 6.36 kWh/kg H2O, and the total amount of energy required for the drying process of 92977.11 kJ/kg dry matter. For comparison, an estimated calculation of apple pomace drying in a rotary dryer was made, which showed the advantage of the filtration method.
The main parameters of the dried material and the briquetted solid fuel sample made from it were studied using calorimetric combustion. The higher calorific value (≈ 18592 kJ/kg and ≈ 19438 kJ/kg, respectively), residual moisture content (< 1 % wt.), and ash content (≈ 0.82 % wt. and ≈ 0.55 % wt., respectively) were determined. The compliance of the characteristics of the produced briquettes with the requirements of existing European standards for solid fuels is shown.
The estimated calculation indicates that the value of the energy consumed for the preliminary preparation of 1 kg of initial raw material exceeds the potential energy that can be obtained by burning 1 kg of the resulting fuel by approximately 79.09%. This balance can be corrected by using secondary heat at the factory to dry the raw materials, given that the energy for heating the thermal agent makes up the largest part of the required energy consumption. It is also possible to consider the option of drying wet material in several stages, for example, initial mechanical pressing of moisture and filtration drying to the required moisture content of the raw material.
The use of secondary raw materials of plant origin as solid fuels can become an alternative to the use of slowly renewable or non-renewable fuel sources, solve the problem of accumulating excessive amounts of industrial waste with a limited shelf life and generally improve the environmental situation.
Authors are expressing their gratitude to CADFEM UA LLC, the official distributor of Ansys Inc. in Ukraine, for help with the software licensing.
A | coefficient for determination of the kinetic coefficient in the first conditional drying period | [1/(m °C)] |
G | productivity | [kg/h], [kg/sec] |
H | layer height of the material | [mm], [m] |
K | coefficient in the second conditional drying period | [1/s] |
KτII | refinement coefficient energy consumption for | [-] |
l | removing 1 kg of moisture for the drying process | [kWh/kg H2O] |
m | coefficient for determination of the kinetic coefficient in the first conditional drying period | [-] |
N | drying rate in the second conditional drying period | [kg H2O / kg dry material] |
N | energy amount | [kWh] |
n | coefficient for determination of the kinetic coefficient in the first conditional drying period | [-] |
ΔP | hydraulic resistance of the porous stationary layer | [Pa] |
Q | energy amount | [kJ] |
T | thermal agent temperature | [°C] |
v0 | thermal agent filtration rate | [m/s] |
wc | moisture content | [kg H2O / kg dry material] |
a | kinetic coefficient in the first conditional drying period | [1/m] |
η | kinetic coefficient in the first conditional drying period | [1/s] |
τ | time | [s] |
χ | relative drying coefficient | [-] |
cr | critical |
e | equilibrium |
lab | laboratory |
recommend | recommended |
t.a. | thermal agent |
Preparation of an alternate solid fuel from alcohol distillery stillage ,Vopr. Khim. Khim. Tekhnol. , Vol. 1 ,pp 54–59 , 2022, https://doi.org/https://doi.org/10.32434/0321-4095-2022-140-1-54-59
, Research of solid fuel briquettes obtaining from brewer’s spent grain ,Journal of Chemistry and Technologies , Vol. 30 (2),pp 216-221 , 2022, https://doi.org/https://doi.org/10.15421/jchemtech.v30i2.256749
, Using coffee production waste as a raw material for solid fuel ,Journal of Chemistry and Technologies , Vol. 30 (4),pp 588-594 , 2022, https://doi.org/https://doi.org/10.15421/jchemtech.v30i4.265116
, Development of dietary fibre enriched chicken sausages by incorporating corn bran, dried apple pomace and dried tomato pomace ,Nutrition & Food Science , Vol. 46 (1),pp 16–29 , 2016, https://doi.org/https://doi.org/10.1108/nfs-05-2015-0049
, Development of fibre enriched chicken nuggets by incorporating wheat bran and dried apple pomace ,Indian Journal of Poultry Science , Vol. 51 (3),pp 312 , 2016, https://doi.org/https://doi.org/10.5958/0974-8180.2016.00052.0
, Impingement drying for preparing dried apple pomace flour and its fortification in bakery and meat products ,Journal of Food Science and Technology , Vol. 52 (9),pp 5568–5578 , 2014, https://doi.org/https://doi.org/10.1007/s13197-014-1680-4
, Apple Pomace in gluten-free formulations: Effect on rheology and product quality ,International Journal of Food Science & Technology , Vol. 50 (3),pp 682–690 , 2014, https://doi.org/https://doi.org/10.1111/ijfs.12662
, Effect of apple pomace on quality characteristics of brown rice based Cracker ,Journal of the Saudi Society of Agricultural Sciences , Vol. 16 (1),pp 25–32 , 2017, https://doi.org/https://doi.org/10.1016/j.jssas.2015.01.001
, Evaluation of apple pomace biochemical transformation to biofuels and pectin through a sustainable biorefinery ,Biomass and Bioenergy , Vol. 172 ,pp 106757 , 2023, https://doi.org/https://doi.org/10.1016/j.biombioe.2023.106757
, Valorization of Apple pomaces for biofuel production: A biorefinery approach ,Biomass and Bioenergy , Vol. 142 ,pp 105785 , 2020, https://doi.org/https://doi.org/10.1016/j.biombioe.2020.105785
, Bioethanol production from Apple Pomace left after juice extraction ,The Internet Journal of Microbiology , Vol. 5 (2), 2008, https://doi.org/https://doi.org/10.5580/3a8
, Supplementation of carbon-based conductive materials and trace metals to improve biogas production from Apple Pomace ,Sustainability , Vol. 13 (17),pp 9488 , 2021, https://doi.org/https://doi.org/10.3390/su13179488
, Biogas generation Apple Pulp ,Bioresource Technology , Vol. 100 (17),pp 3843–3847 , 2009, https://doi.org/https://doi.org/10.1016/j.biortech.2009.03.012
, Energy production from anaerobic co-digestion processing of cow slurry, olive pomace and Apple Pulp ,Renewable Energy , Vol. 83 ,pp 1043–1049 , 2015, https://doi.org/https://doi.org/10.1016/j.renene.2015.05.056
, Thermal self-sustainability of biochar production by pyrolysis ,Journal of Analytical and Applied Pyrolysis , Vol. 91 (1),pp 55–66 , 2011, https://doi.org/https://doi.org/10.1016/j.jaap.2011.01.001
, Apple-biowaste-derived hard carbon as a powerful anode material for na-Ion Batteries ,ChemElectroChem , Vol. 3 (2),pp 292–298 , 2015, https://doi.org/https://doi.org/10.1002/celc.201500437
, Biopolymer Poly-Hydroxyalkanoates (PHA) production from Apple Industrial Waste Residues: A Review ,Chemosphere , Vol. 284 ,pp 131427 , 2021, https://doi.org/https://doi.org/10.1016/j.chemosphere.2021.131427
, Development of bio-based films and 3D objects from Apple Pomace ,Polymers , Vol. 11 (2),pp 289 , 2019, https://doi.org/https://doi.org/10.3390/polym11020289
, Processing of apple pomace for bioactive molecules ,Critical Reviews in Biotechnology , Vol. 28 (4),pp 285–296 , 2008, https://doi.org/https://doi.org/10.1080/07388550802368895
, Research into Kinetics of Filtration Drying of Alcohol Distillery Stillage ,Vopr. Khim. Khim. Tekhnol. , Vol. 4 ,pp 58–65 , 2021, https://doi.org/https://doi.org/10.32434/0321-4095-2021-137-4-58-65
, Kinetic regularities of the filtration drying of barley brewer’s spent grain ,Chemistry & Chemical Technology , Vol. 18 (1),pp 66–75 , 2024, https://doi.org/https://doi.org/10.23939/chcht18.01.066
, Simulation of the thermal agent movement hydrodynamics through the stationary layer of the alcohol distillery stillage ,Case Studies in Chemical and Environmental Engineering , Vol. 9 ,pp 100566 , 2024, https://doi.org/https://doi.org/10.1016/j.cscee.2023.100566
, Valourization of using efficiency of filtration drying for alcohol distillery stillage ,Case Studies in Chemical and Environmental Engineering , Vol. 10 ,pp 100820 , 2024, https://doi.org/https://doi.org/10.1016/j.cscee.2024.100820
, - ANSYS, Inc., 20132024, www.ansys.com., Accessed
CFD simulations of membrane filtration zone in a submerged hollow fibre membrane bioreactor using a porous media approach ,J. Membr. Sci. , Vol. 36 (1-2),pp 57–66 , 2010, https://doi.org/https://doi.org/10.1016/jmemsci.2010.07.008
, Turbulence model choice for the calculation of drag forces when using the CFD method ,J. Biomech. , Vol. 43 (3),pp 405–411 , 2010, https://doi.org/https://doi.org/10.1016/j.jbiomech.2009.10.010
, - , Jacaranda Physics 1 VCE Units 1 and 2 Fourth edition LearnON and Print, John Wiley & Sons Australia, Ltd, 2019
- , Drying in the Process Industry, 2012
- , Handbook of Industrial Drying, 2014
Thermophysical properties of fruit ‒ a review with reference to postharvest handling ,Journal of Food Measurement and Characterization , Vol. 14 ,pp 2917–2937 , 2020, https://doi.org/https://doi.org/10.1007/s11694-020-00536-8
, Expansion of the range of wet air i-D diagram for Environmental Safe Heat Production ,Environmental Safety and Natural Resources , Vol. 26 (2),pp 15–22 , 2018, https://doi.org/https://doi.org/10.32347/2411-4049.2018.2.15-22
, A review of European standards for Pellet Quality ,Renewable Energy , Vol. 36 (12),pp 3537–3540 , 2011, https://doi.org/https://doi.org/10.1016/j.renene.2011.05.013
,